Table of Contents
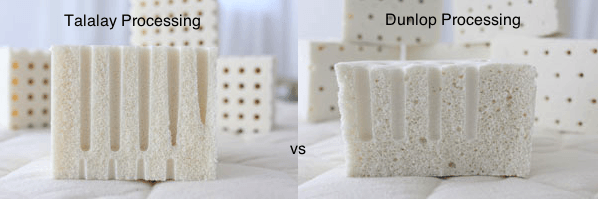
Talalay latex processing produces a more consistent air bubble or “cell structure.” The Dunlop latex process produces a more erratic cell structure, with the foam slightly denser on one side. The Talalay process is more elaborate and needs more steps and non-toxic ingredients. It is also more expensive to produce. The performance and comfort differences between the two are almost imperceptible.
Uh oh! You’re out gathering information about natural mattresses and realize you have a crucial descision to make. Talalay latex or Dunlop latex.
Let’s break down the different facets of this question.
The natural latex manufacturing process
It all starts with Organic Latex, made from the sap of rubber trees that typically grow in southeast Asia. This primary matter is transformed into latex foam using two distinct manufacturing processes: Dunlop and Talalay. Organic Latex pads used in mattresses do not use toxic chemicals, synthetic materials, pesticides, or herbicides. It is important to determine if the manufacturer you choose to buy your mattress uses 100% Organic Latex or a synthetic blend.
Blended latex foam contains both natural and synthetic latex, typically in a proportion of 80% synthetic and 20% natural. Synthetic blend latex foam is less expensive to produce but does not breathe as well as organic and is less durable. Synthetic blend latex foam can also become deformed over time by being compressed in the same place. Latex can be labeled as “natural” even if it contains only 30% natural latex. If you’re looking for completely natural latex with nothing added, make sure the manufacturer labels it as “100% natural latex” or “100% organic latex”.
Look for certifications
Make sure the latex foam in the mattress you are considering is 3rd party certified by either GOLS, Oeko-Tex, or Eco Institut. There are other certifications, but the three mentioned are the most credible. Most reputable natural latex mattress brands have their mattresses certified by at least one of the three certifications.
Dunlop and Talalay refer to the process of converting liquid latex into a solid form.
The Dunlop method has been used since 1929 to “vulcanize” latex.
Talalay processing produces a more consistent air bubble or “cell structure.” The Dunlop process produces a more erratic cell structure, with the foam being slightly denser on one side Usually, the bottom side is denser, as the air bubbles shift to the top after the liquid latex sap is poured into the mold. The Talalay process is more elaborate and needs more steps and non-toxic ingredients. It is also more expensive to produce.
The performance and comfort differences between the two are almost imperceptible. The comfort differences between the two are negligible, and any perceptible difference would only be guided by personal preference.
Most of the mattresses featured on NaturalMattressFinder.com have Dunlop latex. It is super responsive, contouring and durable.
The Dunlop process
This is the time-tested way of converting liquid latex into a usable foam material.
- The liquid latex is emulsified in a giant milk-shake-type blender. This process infuses the liquid latex with tiny little air bubbles.
- The emulsified liquid is poured into a mold that resembles a waffle cooker.
- The lid is closed, and the latex is steam cooked. Thousands of small rods distribute steam evenly in the latex. These rods also leave a perforated pattern that promotes air circulation.
- The latex is baked in about 20-30 min, and the foam is extracted from the mold.
The Talalay process
The Talalay manufacturing process is a more modern way to process natural latex and produces a foam that is less dense than Dunlop foam. This does not mean that it is softer. Talalay foam can be produced in a variety of firmness levels.
- The liquid latex is emulsified in a giant milk-shake-type blender. This process infuses the liquid latex with tiny little air bubbles.
- The emulsified liquid is poured into a mold that resembles a waffle cooker.
- The mold is filled about halfway.
- A non-toxic chemical compound is added to stabilize the air bubbles.
- The air-tight lid of the mold is closed, and the mold is put under vacuum. All the air is sucked out of the mold, and the air bubbles caught in the latex expand. In this step, the latex fills the interior of the mold.
- The latex is then frozen to a temperature of −20 °F (−28 °C), and the air bubbles maintain their position within the foam.
- Carbon dioxide is pushed through the foam. The chemical reaction causes the foam to gel into place and maintain its shape.
- The temperature inside the mold is incrementally increased to 230 °F (115 °C) for a measured amount of time.
- The foam is de-molded and washed. The entire process takes around 60 min.
Depending on the manufacturer, Talalay foam can contain non-toxic adhesives.
For example, Talalay Global, a USA-based foam manufacturer, uses water-based adhesives that contain 6 non-toxic chemicals (acrylate resins, diphenyl diisocyanate, Phenol-melamine resins, Phenol-urea, Polyvinyl acetate, and waxes styrene-butadiene copolymer) and 3 natural materials (fats, Hevea Brasiliensis milk, and water.) in their manufacturing process.
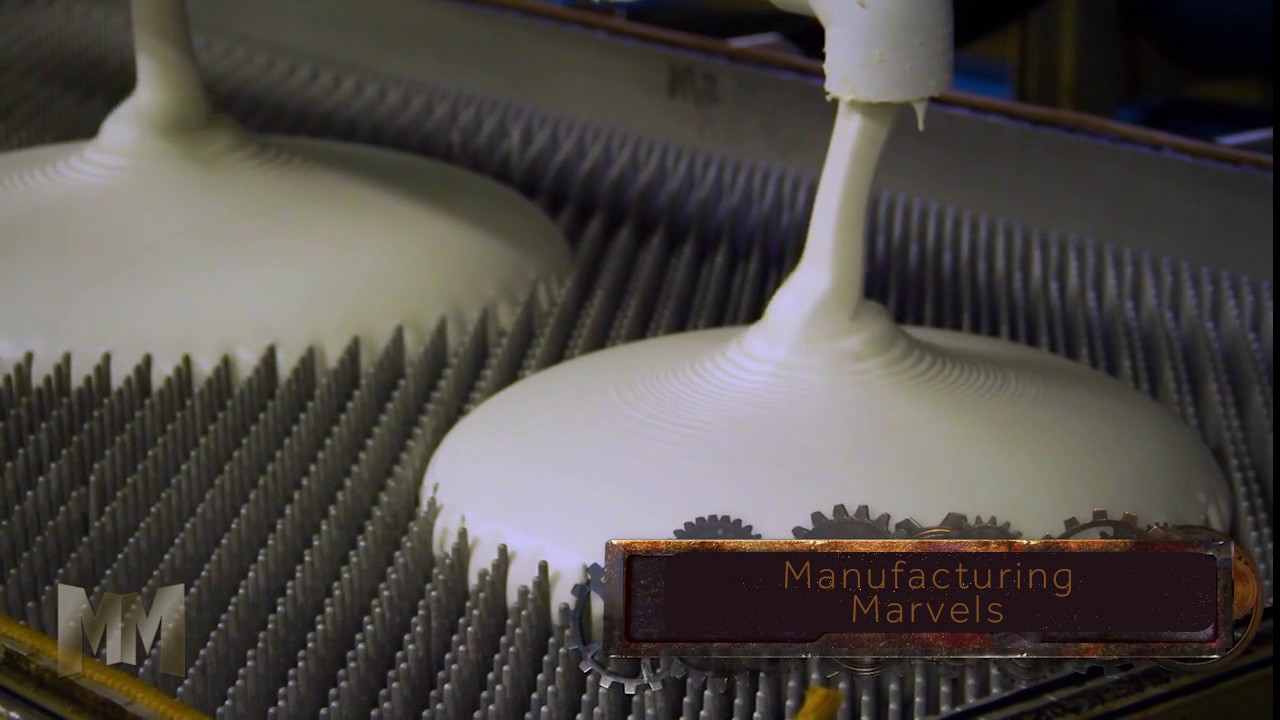
>6 non-toxic chemicals (acrylate resins, diphenyl diisocyanate, Phenol-melamine resins, Phenol-urea, Polyvinyl acetate and waxes styrene-butadiene copolymer
None of those chemicals are non toxic.
A more accurate statement would be:
they are identical to chemicals found in, or used to create, existing furniture.
Acrylate resins?
Glue. Plastic. Etc.
Diphenyl isocyanate?
Thats the precursor for polyurethane. Not PU *foam*, but PU glue
Phenol-melamine is just a particular kind of melamine, probably used in this case as a modifier of other resins, which is used all the time (think the surface of cheap coffee tables, desks, cabinets, dinner tables, etc.).
The Phenol urea is glue. Its actually *phenol urea… FORMALDEHYDE… resin* but furniture manufacturers avoid using the word “formaldehyde” whenever possible and have literally lobbied to make it legal to refer to formaldehyde containing chemicals without mentioning the term, almost as though you would simply assume its there right!?!?!
NOTE: these compounds *DO* release formaldehyde over time (as with most polymerization, cross linking/gelling, etc. the process IS reversible, and there are always unreacted reagents in a cross linked/gelled polymer, no such polymer can go to 100% because the diffusion of cross linking agents or active monomers is eventually impeded as the reaction proceeds…. literally the molecules can’t move around because the stuff turns into a glass or gel that restricts molecular movement)
Polyvinyl acetate is glue
Wood glue. Regular old white elmers glue stuff that your kids eat.
Styrene butadiene copolymer is synthetic rubber/plastic. SBS block copolymer is used to make tires, plastics, etc.
Note that to synthesize all of that information into a succinct statement:
Talay process requires gluing layers of latex foam together to create larger chunks of latex.
Dunlop does not.
Thats basically the distinction.